Lashing refers to the use of steel strapping, chains, steel wire, textile straps, ropes and other securing materials which are fixed, on the one hand, to the package and, on the other hand, to the CTU and then tensioned lightly. The important factors that determine the effectiveness of the lashings are the quality of the materials and the fixing points as well as the directions in which the lashings work. This means that lashing angles also play a critical role. Lashing a package is intended to prevent it from moving longitudinally or laterally and to stop it rising from the loading surface or tipping. A lashing is used to create a tight fit. The term direct lashing is also used. The quantity and thickness of the required lashings will depend on the weight of the load that is to be secured, on the anticipated forces, on the maximum securing load of the lashings and the lashing angles. More information can be found in the relevant sections dealing with the materials and in the lashing examples. Lashing has a less important role to play when securing packages in box containers. Since the lashing points in the container usually have a maximum securing load of 1,000 daN (corresponds to a mass of approximately 1 t), the use of lashing must be restricted to lighter packages. Another consideration is the fact that lashing points are often not accessible as a result of spatial restrictions and the space occupied by packages. When securing loads in open top containers a higher MSL can generally be assumed - often in the region of 2,000 daN (corresponds to a mass of approximately 2 t). Platform-style containers, on the other hand, offer good lashing facilities, which means that lashing is virtually indispensable on such cargo transport units.
|
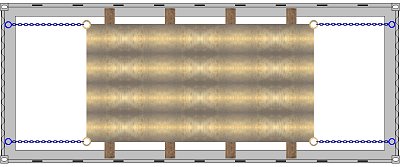 |
|
Horizontal lashings with longitudinal components - View from the top |
|
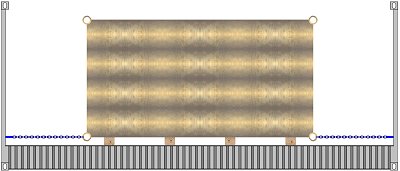 |
|
Horizontal lashings with longitudinal components - View from the side |
Horizontal lashings have no vertical component. Horizontal lashings attached longitudinally, as shown here, have no lateral components. The package is simply held in place longitudinally by this type of load securing.
|
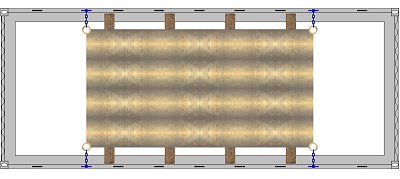 |
|
Horizontal lashings with horizontal components - View from the top |
If the lashings are absolutely parallel to the horizontal transverse axis, they will have no longitudinal or vertical components. A package secured in this manner is thus exclusively secured in the transverse direction. The lashing shown here, however, also has a slight vertical component as a result of the position of the lashing points.
|
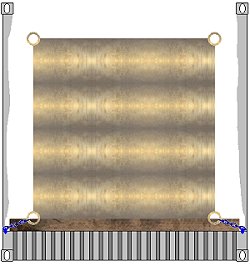 |
Horizontal lashing with transverse and vertical components - Lateral view |
|
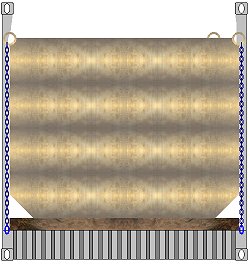 |
Vertical lashing without horizontal components - Lateral view |
A purely vertical lashing has no horizontal component at all. These lashings are thus unable to exert either a longitudinal or a transverse securing effect. Longitudinal and transverse forces can cause the load to move. If this happens, the purely vertical lashings are displaced sideways and sometimes placed under considerable tension. The tension that is created as a result of the load moving exerts a force on the load pushing it down on the container floor. This increases the frictional forces on the floor. Frictional forces for each lashing are calculated using the product of the MSL and the friction coefficient.
|
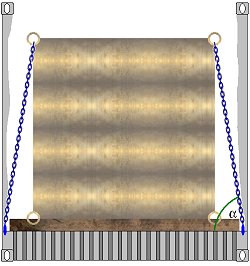 |
Vertical lashings with slight horizontal transverse components - Lateral view |
The German VDI guidelines refer to lashings of this type as inclined lashings. Such lashings form a lashing angle with the horizontal plane, which is referred to as α.
|
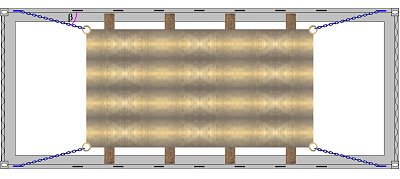 |
|
Diagonal lashings with horizontal longitudinal and transverse components and vertical components - View from the top |
|
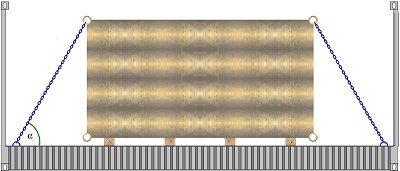 |
|
Diagonal lashings with horizontal longitudinal and transverse components and vertical components - View from the side |
Diagonal lashings form a lashing angle α with the horizontal plane and a further lashing angle β with the horizontal longitudinal direction of the transport unit. According to the terms defined by the VDI, lashings of this type are referred to as diagonal lashings. With the diagonal lashings shown here, the vertical components are the greatest. The horizontal longitudinal components are considerably smaller, and the horizontal transverse components even smaller still. Cross lashings are simply a special form of diagonal lashing. These are advantageous if the lack of space requires greater horizontal components.
|
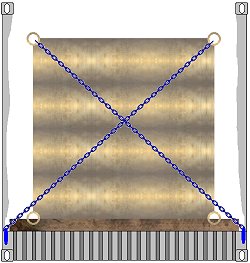 |
Cross lashings with horizontal and vertical components - Lateral view |
 |
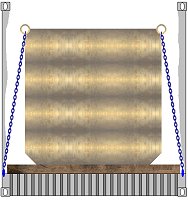 |
 |
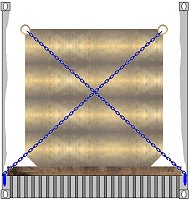 |
|
Diagonal lashings with small horizontal transverse components |
|
Cross lashings with better horizontal transverse components |
The package on the right is considerably better secured laterally than the one on the left. Under such conditions cross lashings are often suitable. But beware: This no longer applies if the package is to be secured against tipping.
 |
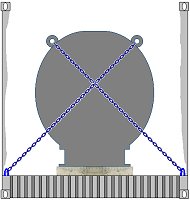 |
 |
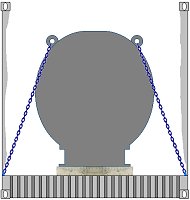 |
|
Ineffective components for securing against tipping |
|
Effective components for securing against tipping |
|
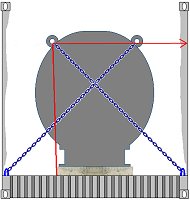 |
|
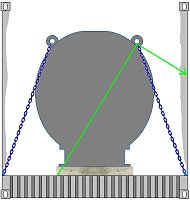 |
|
Optimum lashing angle to protect against tipping, but impossible to implement |
|
The real lashing angle is close to the optimum to protect against tipping. |
The optimum angle for securing against tipping is to imagine a line to the outside at right angles to the line connecting the lashing point and the tipping edge:. A clear warning must be issued against the so-called round turn lashings where the lashing material is fixed at one side, wrapped around the object and then fixed at the other side:
 |
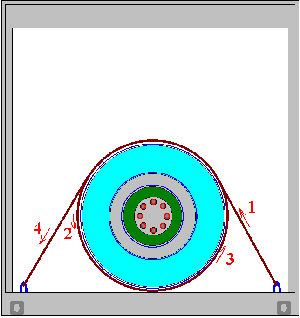 |
Round turn lashing |
Round turn lashings allow the loads to move freely.
 |
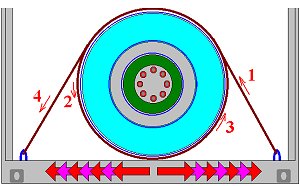 |
Round turn lashings are similar to the diabolo toy principle |
Loop lashings are unfortunately rarely used as a form of tight-fit securing although they are extremely effective. This method can be used very effectively with all long, cylindical loads.
 |
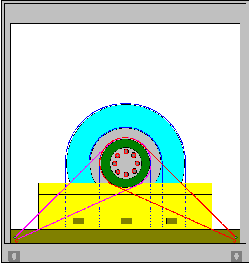 |
Loop lashing used to secure a piece of machinery - Lateral view |
 |
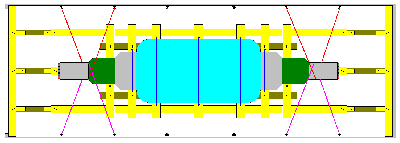 |
|
Loop lashing used to secure a piece of machinery - View from the top |
 |
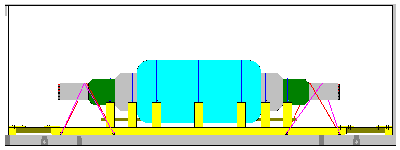 |
|
Loop lashing used to secure a piece of machinery - Side view |
Loop lashings can be used anywhere where the lashing can be wrapped around a component of the load. To create a loop lashing, the lashing material is fixed to a lashing point on the means of transport, wrapped around the load and back to the side it started from and, if possible, secured to a second lashing point.
When using separate lashing points, the permitted lashing force of a single strand of the lashing can be increased by a factor of up to two at best. With a lashing point with a permitted load of 2,000 daN (approximately 2 t) and a permitted lashing force of a single strand of lashing material of 2,000 daN (approximately 2t) as well, this will result in a maximum of 4,000 daN (approximately 4 t) securing force. The opening angle between the ends of the lashing material leads to a certain reduction: With a maximum possible angle of 90° in the three diagrams this is 30%. The pretensioning force in the lashing will also reduce the securing force. However, depending on the circumstances, the frictional forces may be increased. There are numerous possible variations on the loop lashing principle. A little imagination and experience will show that this principle can be used to solve a multitude of load securing problems. The weaknesses of the round turn lashing and the strengths of the loop lashing have been investigated by the Fortbildungszentrum Hafen Hamburg (the training center at the port in Hamburg) in a very effective test. Part of this series of photos is shown here:
|
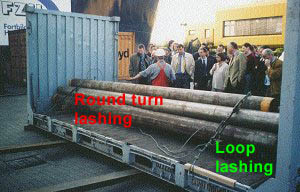 |
The lashings have been applied - The tipping process begins. |
|
An angle less than 30° has been reached - part of the friction forces are still effective. |
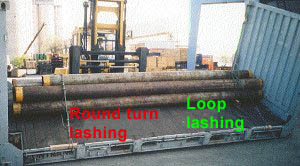 |
|
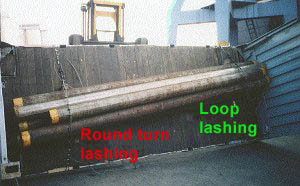 |
The round turn lashing fails, the loop lashing remains firm. |
|
Impact: The round turn lashing fails even more, the loop lashing still remains firm! |
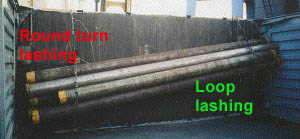 |
If there are no securing points, lashings can be attached with "head loops".
|
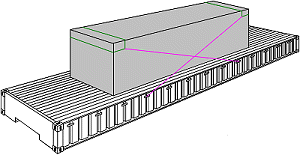 |
Head loops with spring lashings in the form of a cross lashing |
Note that the lashing shown in this sketch is not sufficient for carriage. It is only shown to illustrate the principle of head loops (green) and lashings attached to them (magenta). Securing using head loops will usually require two members of staff. This method is much too time-intensive to implement alone. The term spring lashing is used to described lashings that run from the outside to the inside, regardless of whether they cross. Head loops can take a number of different forms. This Container Handbook and the GDV Cargo Securing Manual contain a number of samples in the various examples.
|
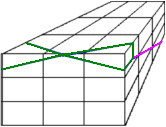 |
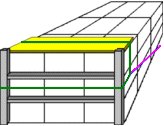 |
|
Figure of eight head loop |
Head loop with padding |
If layered goods run the risk of the head loop cutting in between the individual packages, then a figure of eight head loop can be used to achieve the same result. The use of the head loop as shown above, requires the packages to be stable enough to take the full MSL of the lashing. If this is not the case, boards, lattices, walking boards, square lumber dunnage and other similar aids can be used to cushion them in order to meet the prerequisites for the head loops. This is usually needed when securing bundles, IBCs, units, bagged cargo pallets, or other similar packages. The majority of securing errors are made when making and securing the lashings. This picture shows the use of a hook which has already been bent open, and which has also been inserted in the wrong direction. The chain tensioner shown has not been used correctly. It must be tightened down by at least 45° and must not protrude at right angles as shown here, otherwise there is a danger that the link of the chain could escape from the lug of the tensioner. The lashing angles are not suitable. High vertical components have been achieved, but the longitudinal and transverse components are too low.
 |
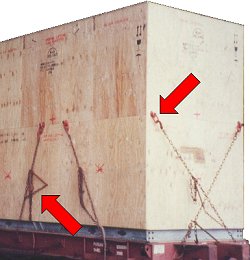 |
Faulty fixing and errors |
 |
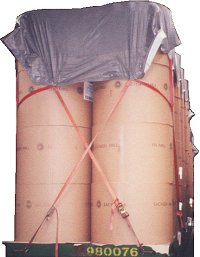 |
Tight-fit securing of rolls of paper using a WisaFix lashing cover |
This example shows the use of a load securing tarpaulin with textile straps that have been secured to the ends of the roll trailer, thus ensuring a tight-fit. This type of securing is only suitable for ocean-going transport if the roll trailers are stowed in a "tight-fit" constellation next to each other and either along the length of the ship or athwartships. Since the load has simply been strapped down at the sides of the roll trailer, the securing is sufficient for terminal transport, but not for ocean-going transport.
|