Continued from Section 4.1.2.2: The influence of faulty unitization and palletization on load securing According to the IMDG code, the unit loads should be compact, have as regular a form as possible, and for the most part, vertical sides. The top of the unit load should be level. It must be possible to stack the unit loads. They must be constructed and secured in such a way that it is unlikely that the individual packages can become damaged.
 |
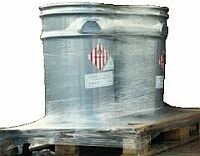 |
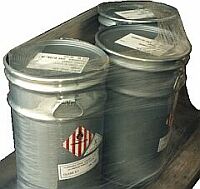 |
|
This unit load does not comply with the IMDG code |
The requirements of the IMDG code have not been met. Nor have they been met by the following unit loads:
 |
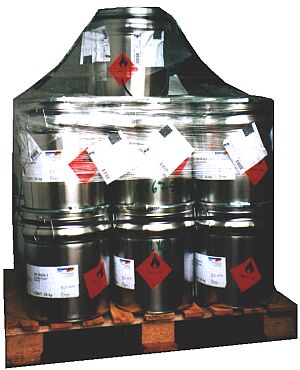 |
The main faults are:
No firm bond to the pallet, pallet is not loaded flush, unit cannot be stacked. |
 |
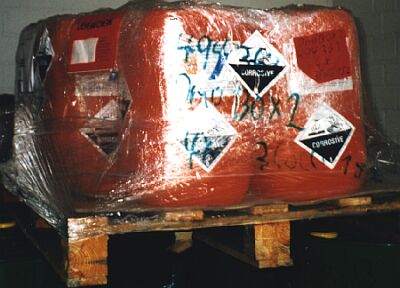 |
|
Load unit that does not comply with the regulations |
 |
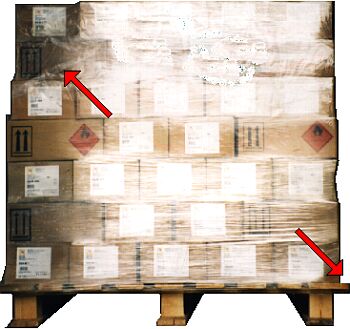 |
|
Load unit that does not comply with the regulations |
This pallet carrying hazardous goods is not packed flush. The bond to the pallet is not secure enough and there is a large gap in the top layer.
 |
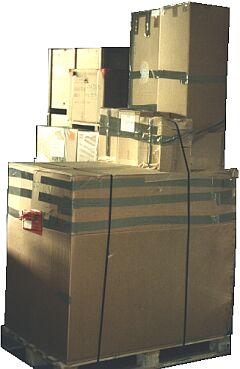 |
Irregularly shaped unit loads hinder packing work. |
Unit loads that are as irregularly shaped as the one shown here make packing work more difficult. It may be necessary to split this unit and to load the packages individually.
 |
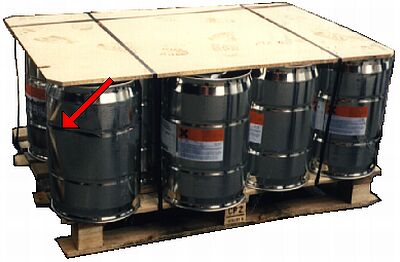 |
|
The projection of the load beyond the edges of the pallet is a potential source of damage |
One of the drums was already dented when the pallet was delivered by truck because the load extends beyond the edge of the pallet. Part of the strapping had become loose and the lid had shifted slightly. It will only be possible to transport this load without damage by investing a considerable amount of effort for load securing. Since this load comprises Class 8 hazardous goods for maritime transport, this marks a violation of the law.
 |
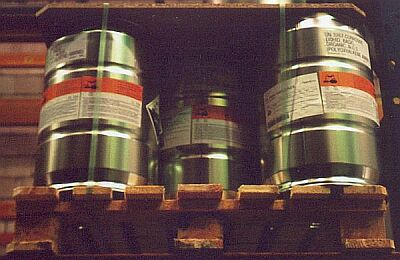 |
|
Loading gaps and faulty strapping increase the risk of damage. |
The violation of the law is even more obvious here:
 |
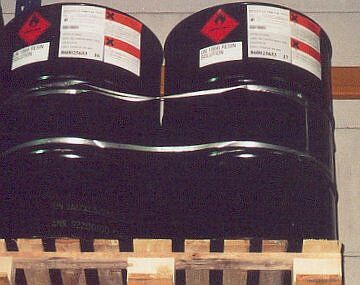 |
|
Insufficient strapping - no bond to the pallet |
This cannot be termed a unit load. The drums must be loaded individually. There are no bounds to some people's imagination when it comes to dreaming up methods of forming unit loads. The few pictures below should serve to illustrate the problem.
Damage is inevitable if loads are packed into a container in this state. Unless, of course, a huge amount of work and materials are invested during handling to repack, improve the packaging and to secure the load in place safely.
In place of the outlay required to unpack the pallets, dispose of the wrapping film, and to then pack the items properly and secure them in the container etc. it would possibly be worthwhile to procure a (used) box pallet or case and load the pails in that. It should also be borne in mind that such a breach of regulations would incur a fine if the authorities were to carry out an inspection.
 |
Above and right: Faulty formation of unit loads - Violation of loading guidelines |
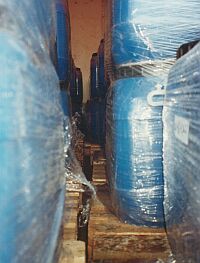 |
These plastic drums also are not firmly secured to their pallet by the wrap. The gaps between the unit loads are an obvious violation of the regulations for the transportation of hazardous goods.
 |
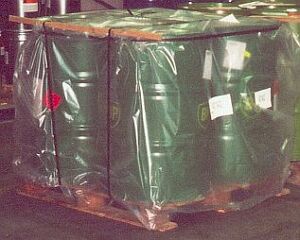 |
|
Incomplete strapping |
The strapping is missing on two sides and on the lower and middle sections of the load. The existing strapping is badly placed. The edge protectors used are only partially effective in this case and they are missing on the other two sides of the pallet. If the film that has been used is a shrink cover then the packers forgot to put the pallet in the shrink oven as well.
 |
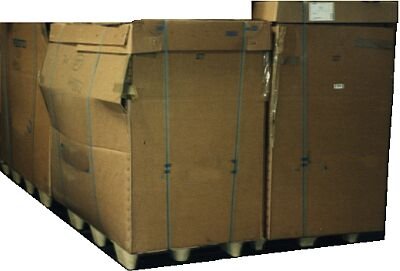 |
|
Unit that is unable to withstand a significant load |
The use of weak packaging hinders the efficient packing of containers. Additional measures for damage prevention are required. Not only that, no edge protectors were used when strapping the load.
 |
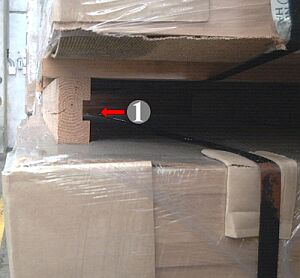 |
|
Rectangular dunnage placed on edge is liable to collapse. |
This rectangular dunnage has been used incorrectly: Here a groove can been seen that has been cut specifically to take steel straps or plastic strapping in order to ensure that the strapping does not break or tear when it comes into contact with the floor. Used incorrectly as we can see here, the dunnage is likely to collapse. It is also increases the load on the surface it is standing on.
 |
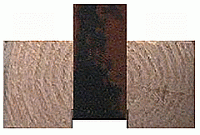 |
 |
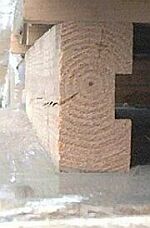 |
|
Correct use of dunnage |
|
Incorrect use of dunnage |
 |
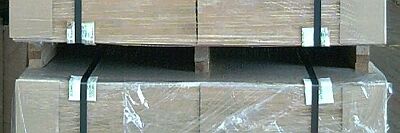 |
|
Risk of damage is increased when dunnage is used on edge. |
The example given below shows the effort that must be invested in order to counteract the problems of faulty packaging and how unsatisfactory the ultimate solution is:
 |
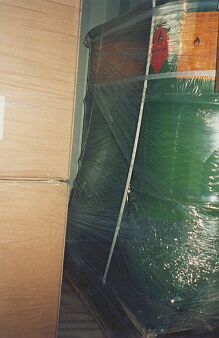 |
Above and left: Unit load that does not comply with the IMDG code |
A number of mistakes have been made in packing this container: The pallet holding the drums has not been loaded hard up against the right-hand container wall. A wooden pallet has been placed vertically between the chipboard pallet and the drum pallet, but this does not fill the gap completely.
 |
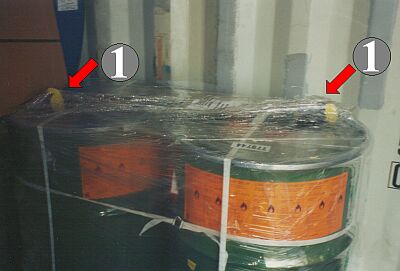 |
|
In violation of the regulations, this load surface is not even. |
The drainage cocks for the drums (1) have been placed on top of the drums and stretch wrapped in place. The only possible way of stacking other items on top of these drums would be to create a level surface using dunnage placed lengthways and then widthwise.
 |
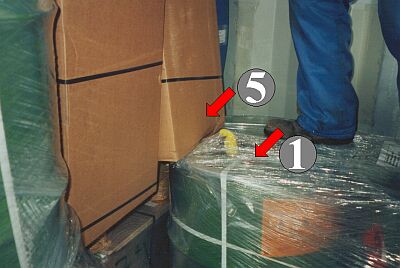 |
|
Risk of drainage cock being damaged by a packer standing on it |
The gap behind the drum pallet must be filled in manually. Since the packer must ensure that he does not stand on the drainage cock, he is unable to handle the heavy carton (5) safely and it is distorted as a result of being accidentally placed on the edge of the drum.
 |
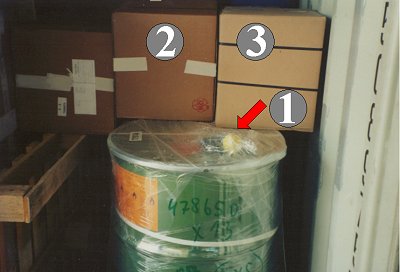 |
|
The shrink-wrapped drainage cocks make packing work more difficult |
The stowage gap above the drum pallet is only partially filled here. Behind package (3) there is a gap because the drainage cock of the second drum is located here.
 |
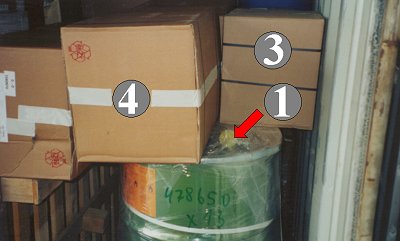 |
|
Packing work is hindered by the shrink-wrapped drainage cocks |
A gap has also been left for drainage cock (1) in front of package (3) and next to package (4). If the drainage cocks had been shrink-wrapped at the bottom of the drums, a wooden board could have been used as interlayer dunnage to allow the remainder of the stowage space in the container to be filled out more efficiently. It is correct and sensible to ensure that the hazardous goods drum pallet is packed in the vicinity of the container doors.
|