 |
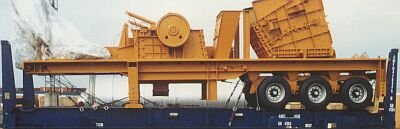 |
|
ausreichend gesicherter Betonbrecher auf einem 40'-Flat |
Bei der Sicherung des Betonbrechers musste ein besonders hoher Material- und Personalaufwand getrieben werden, weil auch hier der Hersteller keinerlei Vorkehrungen für den Transport und die Ladungssicherung getroffen hatte. Einige Bereiche des Fahrzeugs fielen zur Ladungssicherung aus, weil an oder auf ihnen Hydraulik- und Elektroleitungen verliefen. Einige richtig platzierte und ausreichend dimensionierte Zurrpunkte hätten die Ladungssicherungsarbeiten ungemein erleichtert.
|
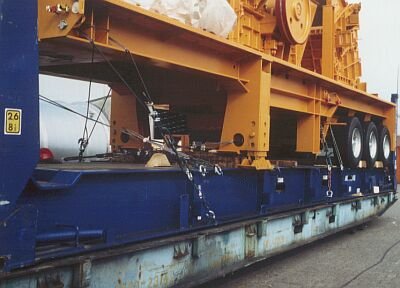 |
|
Schrägansicht einiger Sicherungsmaßnahmen |
An den scharfen Kanten der Brecherbauteile erfahren die Drahtseile eine Schwächung ihrer Einsatzfestigkeit um ca. 50 %. Aufgrund der Konstruktion war eine andere Befestigung nicht möglich.
|
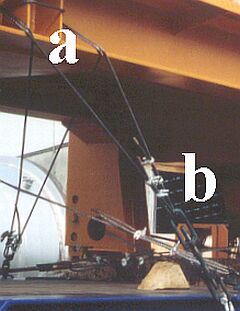 |
konstruktionsbedingte Zurrprobleme |
Um einen homogenen Lasching zu erhalten, hätte bei (a) die Vierfachscherung und bei (b) die Zweifachscherung des Drahtes erfolgen müssen. Aufgrund sehr enger Durchlässe an der Konstruktion war das jedoch nicht möglich. Die Länge der Drähte erschwerte das manuelle Vorspannen. Dadurch wurden beim eigentlichen Vorspannen über die Spannschrauben bereits sehr viele Windungen verbraucht.
|
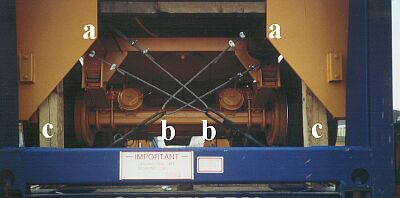
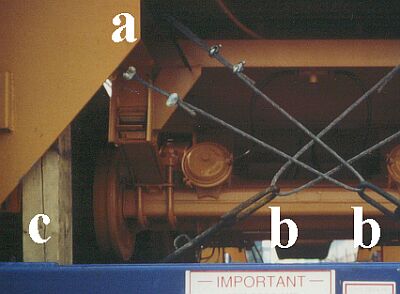 |
|
oben und Ausschnittvergrößerung unten: korrekte Verarbeitung der Drahtseile |
Am hinteren Teil des Fahrzeugs konnten die Drahtseile korrekt angebracht werden. Die Vierfachscherung erfolgt über die scharfen Kanten bei (a), die Zweifachscherung an den Spannschraubenbügeln (b). Positiv ist in der Abbildung das Hochklotzen des Fahrzeugs aus der Federung mithilfe der Kanthölzer (c): So werden unnötige Schwingungen des Fahrzeugs und stoßartige Belastungen der Zurrdrahtseile vermieden.

 |
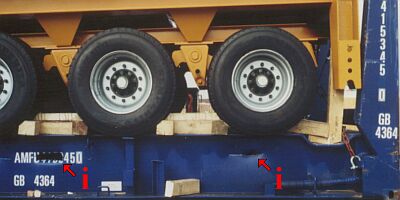 |
|
Längssicherung durch Keilhölzer |
Zur Längssicherung des Fahrzeugs tragen unter anderem die Keilhölzer bei. Auch dieser Aufwand hätte gespart werden können, wenn der Brecher über entsprechende Zurrpunkte verfügt hätte. Mit Schrägzurrungen wäre eine ausreichende Sicherung schnell und kostengünstig realisierbar gewesen. Nicht "gentlemenlike" war die Misshandlung des Flats mit den Gabeln eines Staplers bei (i).
Zur Erstellung stramm sitzender Holzverbindungen gibt es einen kleinen Kniff.
Zuerst werden die beiden Keilhölzer a quer zwischen die Reifen der Achse geschoben. Ein hier nicht abgebildetes Hilfsholz, dessen Länge der Lücke zwischen den Hölzern a entspricht, wird zugeschnitten, zwischen die Hölzer gepasst und mit Treibkeilen gegen die Reifen auseinander getrieben. Die nun etwas vergrößerte Lücke wird ausgemessen und nach diesem Maß wird das Holz b zugeschnitten und eingepasst. Nachdem die Abmessungen für das Sicherungsholz c bestimmt wurden, wird dieses Holz zugeschnitten und gleichfalls eingepasst. Abschließend werden die Treibkeilen losgeschlagen und das Hilfsholz entfernt. Über die Elastizität der Reifen erhält die Holzabsteifung ohne jegliche Nagelverbindung einen festen Sitz.
|
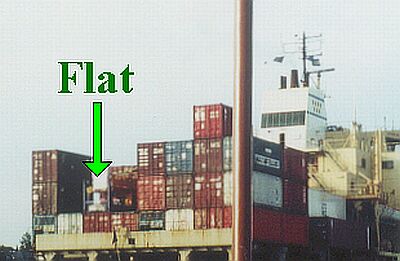 |
|
Stellplatz des Flats an Bord |
Wie wichtig es ist, jede Ladung - auch in Vertikalrichtung - angemessen zu sichern, verdeutlicht dieses Bild. Das Flat steht in der letzten Bay des Schiffes und wird neben den anderen Schiffsbewegungen die größten Vertikalbeschleunigungen beim Stampfen im Seegang erfahren.
|